START FROM SCRAP
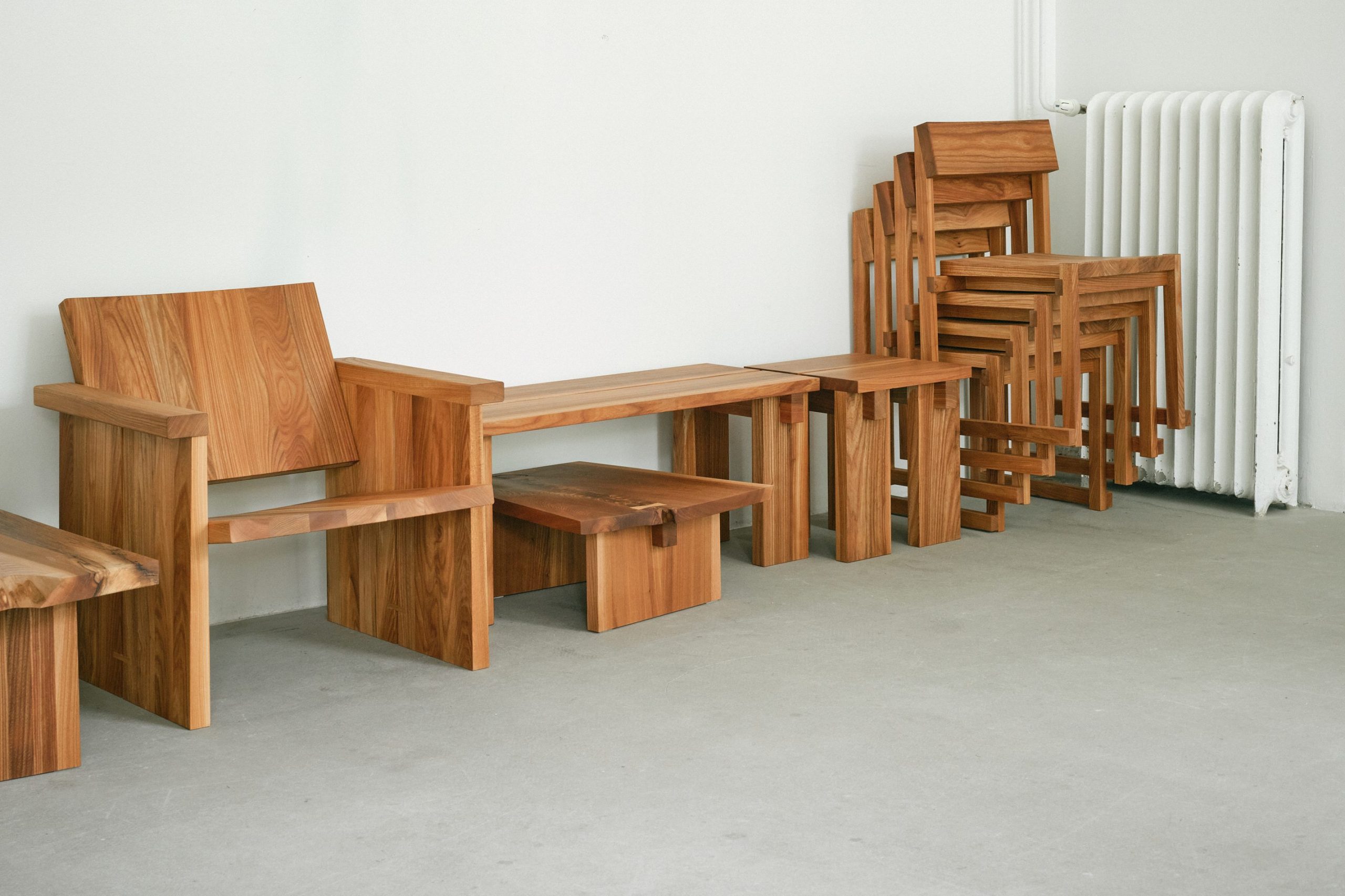
ABOUT CONTEM
Established by childhood friends Cristian Lind and Jack Dalla Santa in Stockholm, Contem emerged from a shared vision rooted in the appreciation for discarded materials.
With a philosophy centered around uncovering beauty in the overlooked, Contem is committed to recontextualizing resources as multi-functional, long-lasting pieces. By giving new life to trees facing the adversity of sickness and working with wood salvaged from demolition sites, Contem strives to create furniture that tells stories of resilience and renewal.

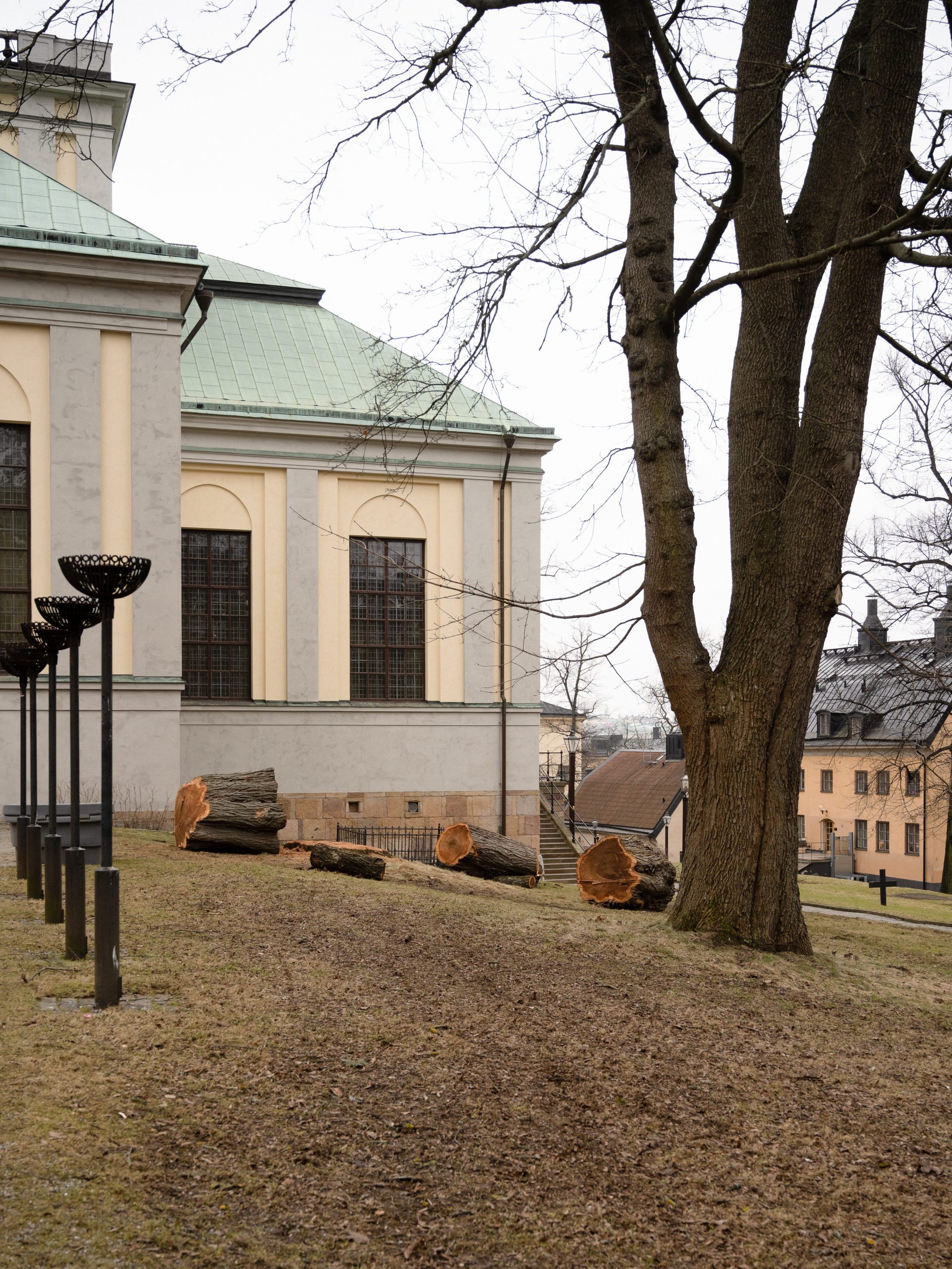
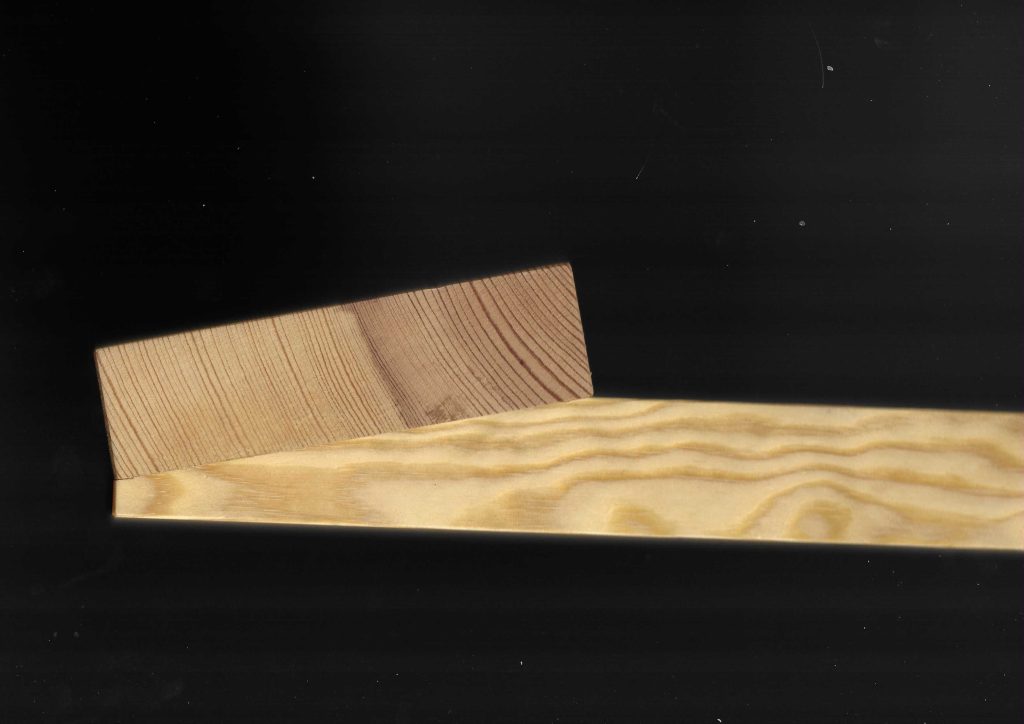
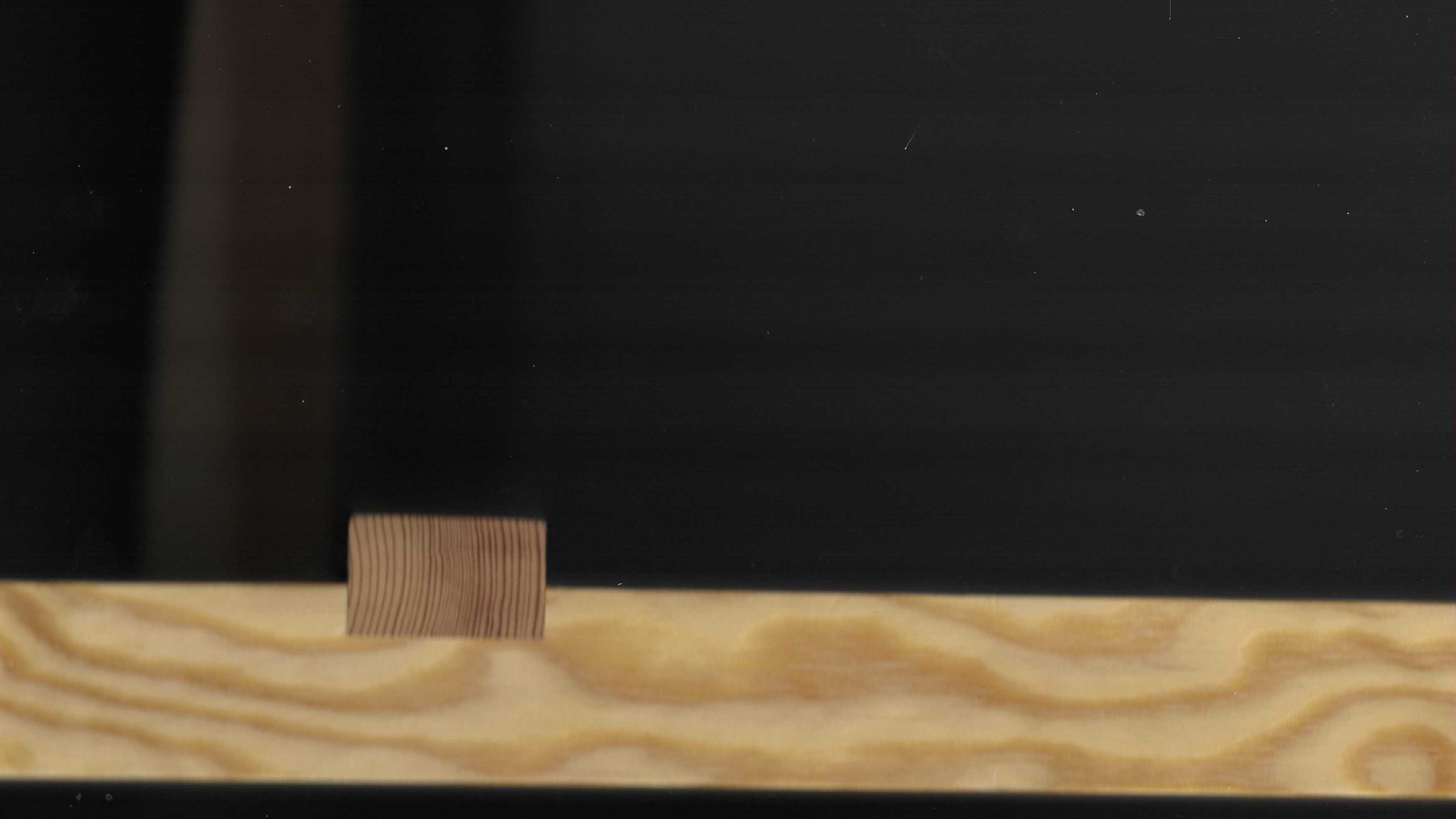
METHOD
We begin our design with the materials at hand. With changing variables, nailing down a process is not the easiest. It’s a collaborative and fluid way of working where things happen simultaneously. For us, it always begins and ends with curiosity — a curiosity for the material, what it can teach us, and who we can work with for the best result. To not make things too abstract, we’ve tried to put this process into words. These are the components forming our method.
SEARCHING
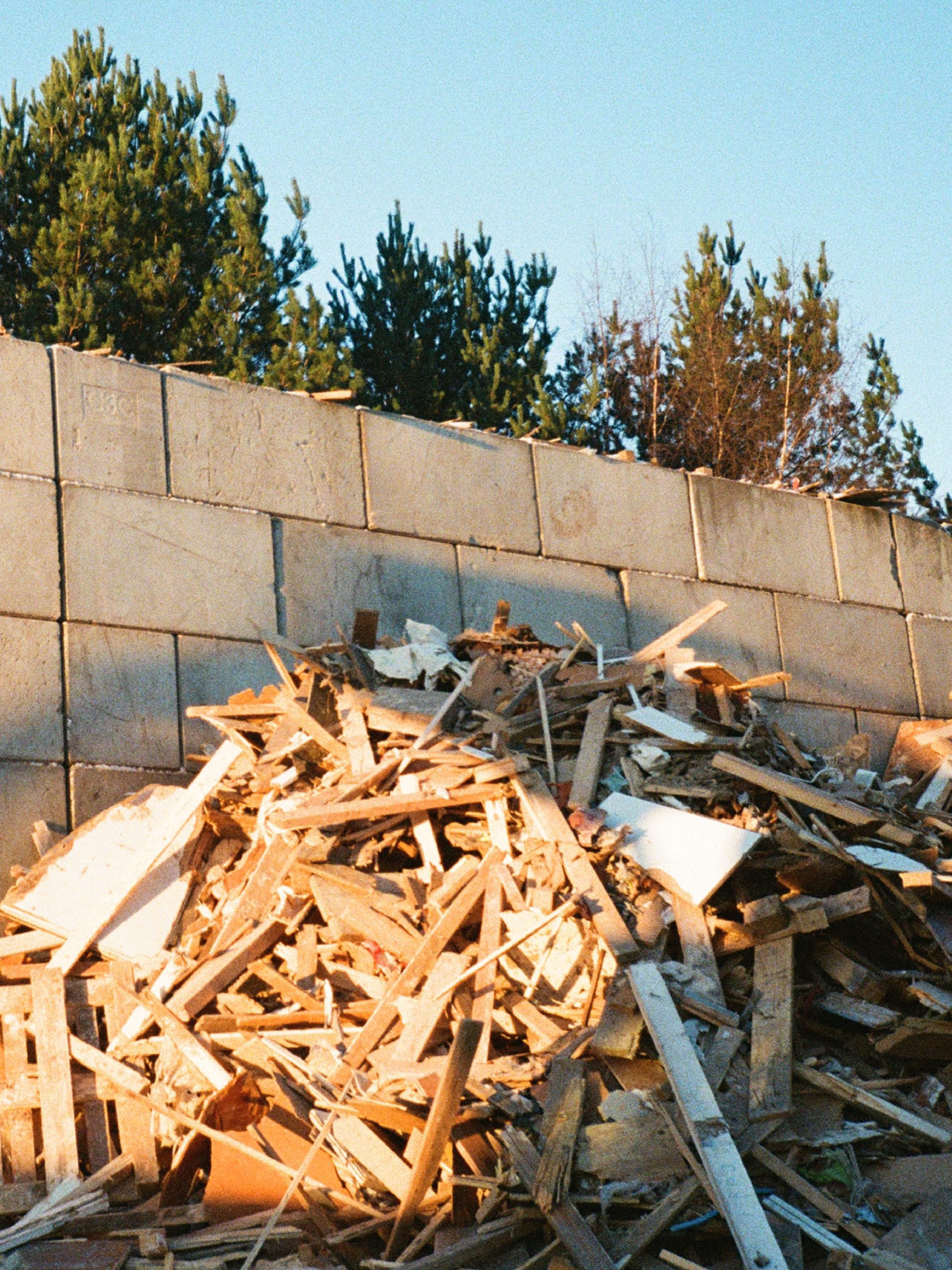
At first, this meant going through crates of scrap wood on the streets and at recycling centres. Now, it’s searching for arborists who only cut down trees if it’s really needed. In the future, it might mean something else entirely. We’re searching for that too.
COLLECTING
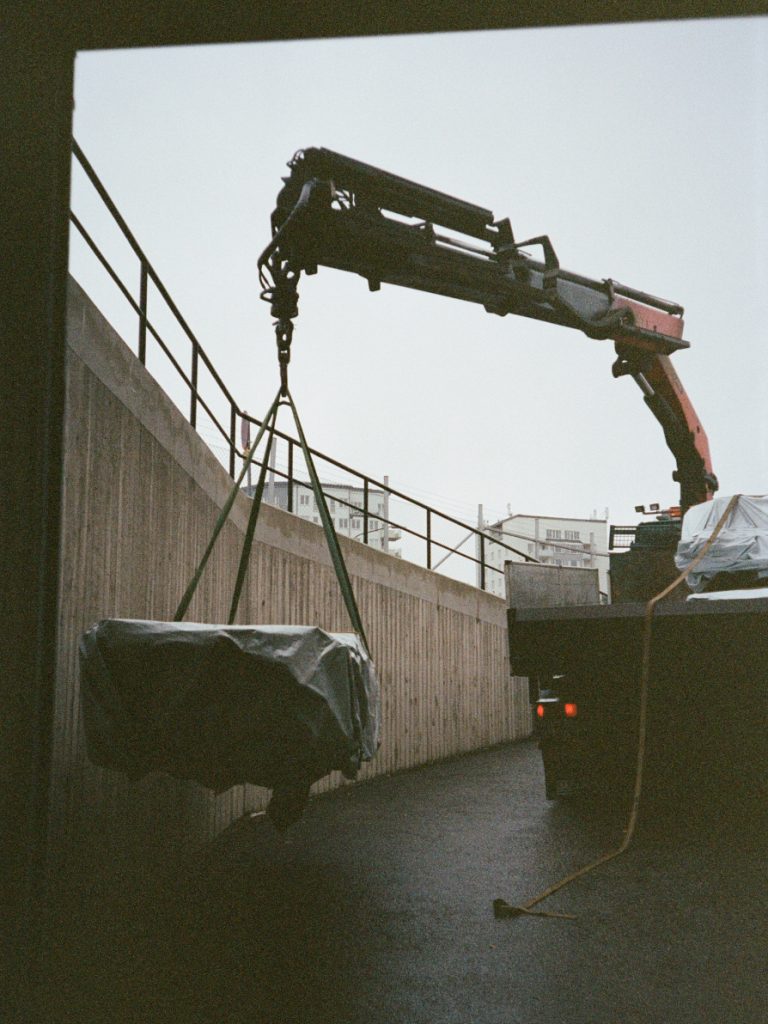
Initially collecting discarded materials in various forms, but also collecting advice from specialists and ideas from furniture makers and designers before us. Collecting is writing down the original coordinates of the trees we use so that what we create is traceable. It’s figuring out how to transport vast amounts of timber in as few runs as possible and assessing what each wooden plank can be used for.
SHAPING
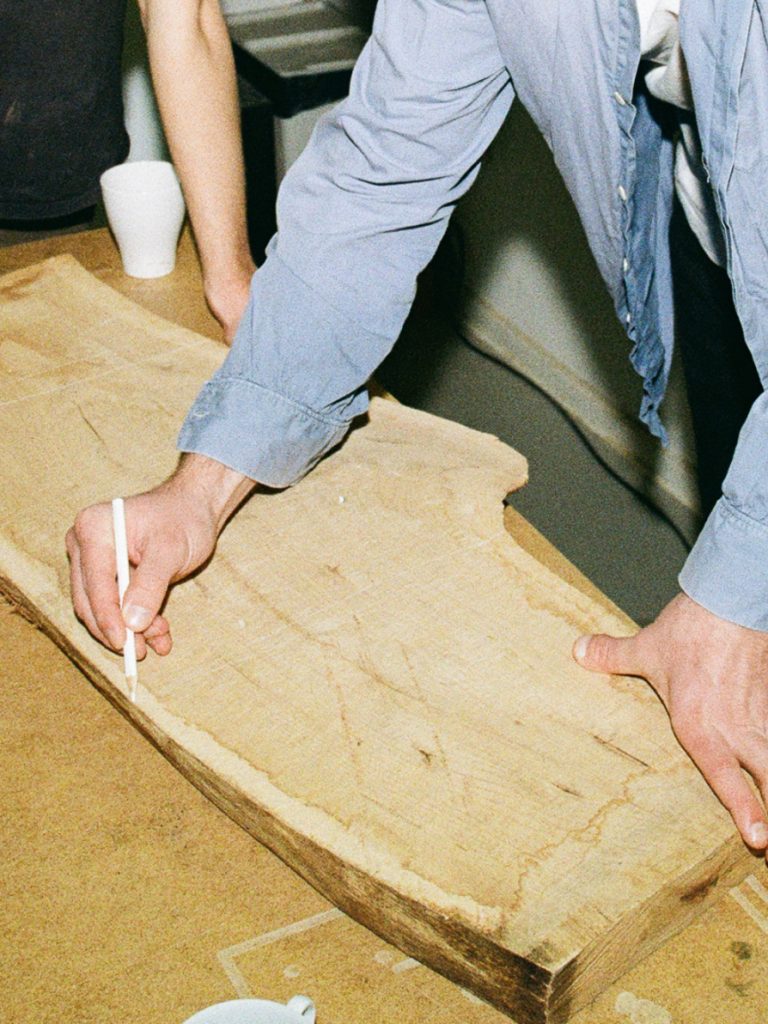
PLACING
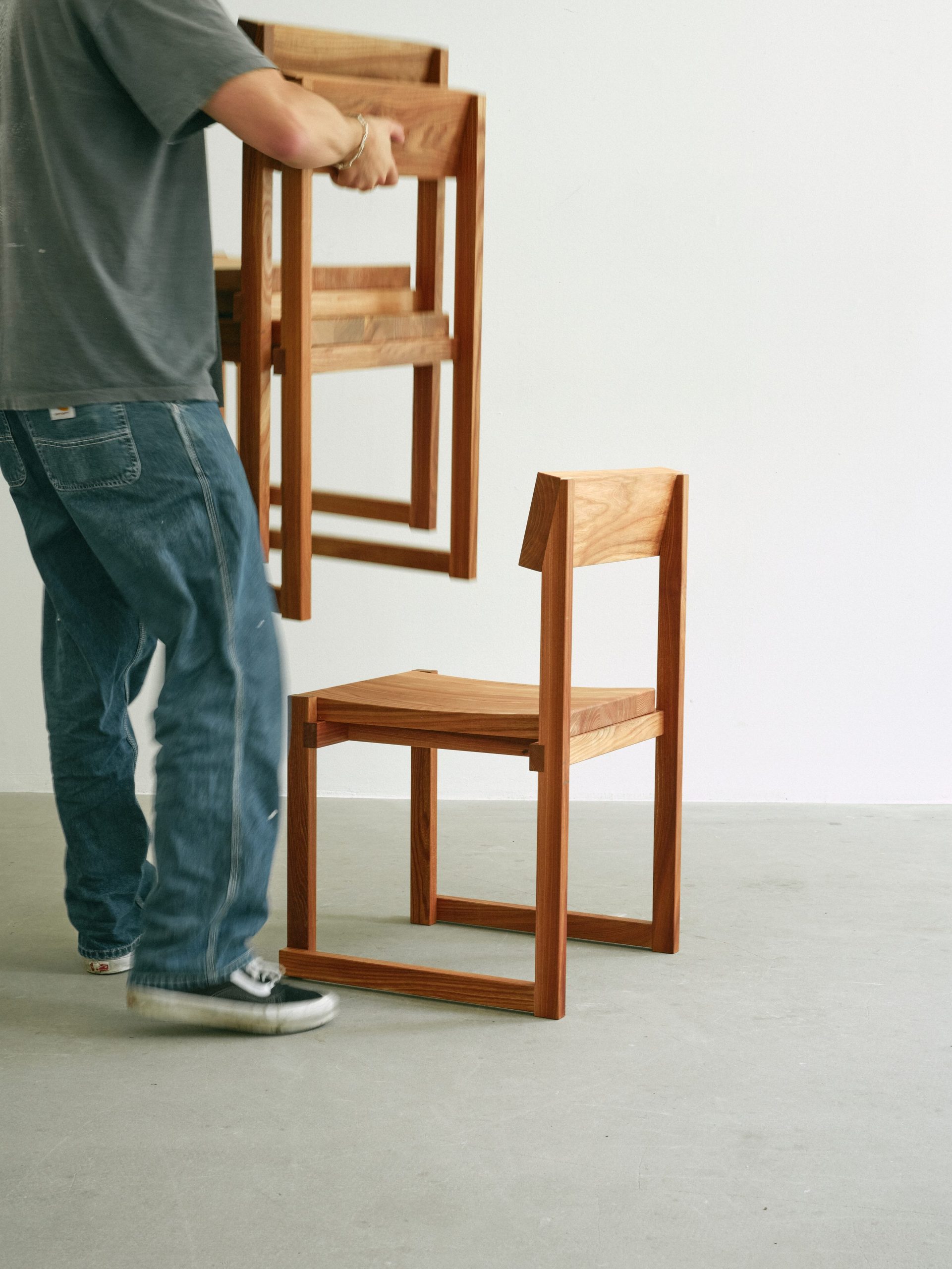
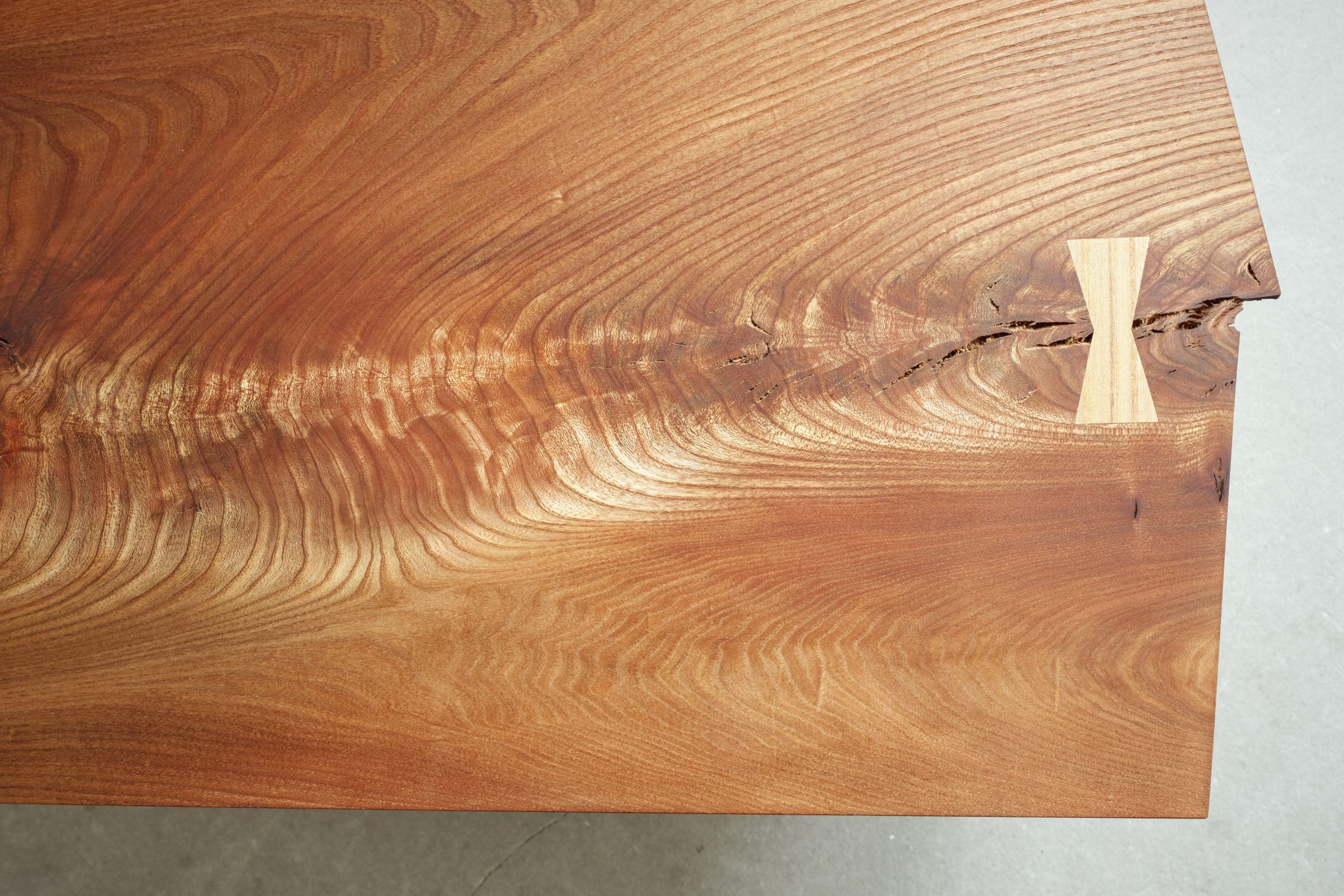
A. COLLECTION
The material for this collection comes from trees infected with Dutch elm disease, which are being cut down to prevent the disease from spreading. The wood is usually burned, but through our production it is repurposed as furniture. We work together with arborists who supply us with the trees, coordinates and documentation. The furniture is produced locally in Stockholm, where we operate, after the wood has been dried. As a hardwood, elm offers both strength and durability, ensuring that furniture crafted from it will stand the test of time. Its warm, inviting color and intricate grain patterns make each piece unique.
The collection’s design is simple and rational, with details that create a rich impression, while maintaining local production. The overall aim is for the material to be the centre of attention.
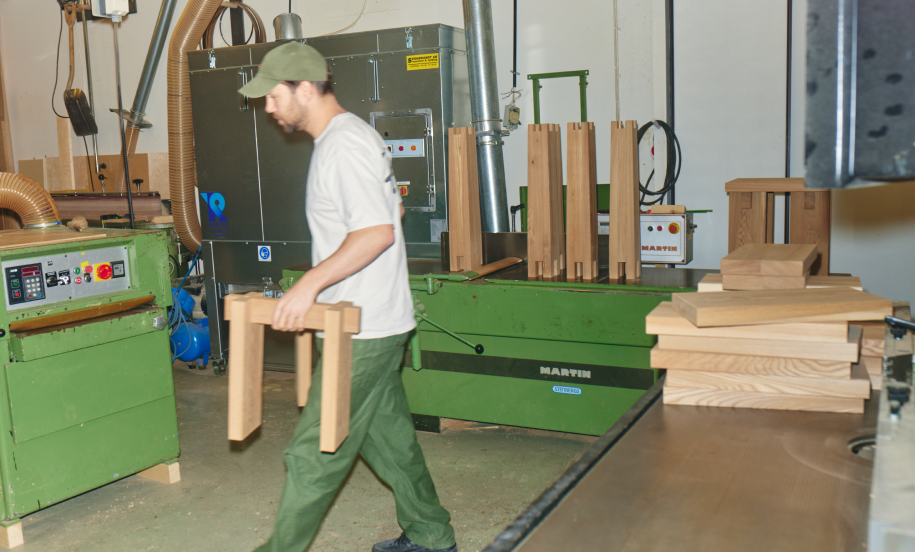